Polished concrete: qualities and differences with other coatings
There is currently a lot of confusion, due to a lack of knowledge, about polished concrete. In fact, most people associate it with the typical industrial style flooring with a strong grey tone and mirror effect that is used in the interiors and exteriors of large surfaces such as offices, shops, factories, warehouses and car parks. Even, although to a much lesser extent, in some private homes.
However, in most cases, what is assumed to be polished concrete is actually microcement. The decorative coating that is currently a trend in interior design and decoration, both in houses and in shops and premises. A coating that has also spread like wildfire on outdoor terraces, facades and swimming pools.
In this article you will find everything you need to know and didn't know about polished concrete: what it is, its main qualities, the different finishes it allows, the application process, the price per square metre and, above all, the main differences with microcement or smoothed microcement.
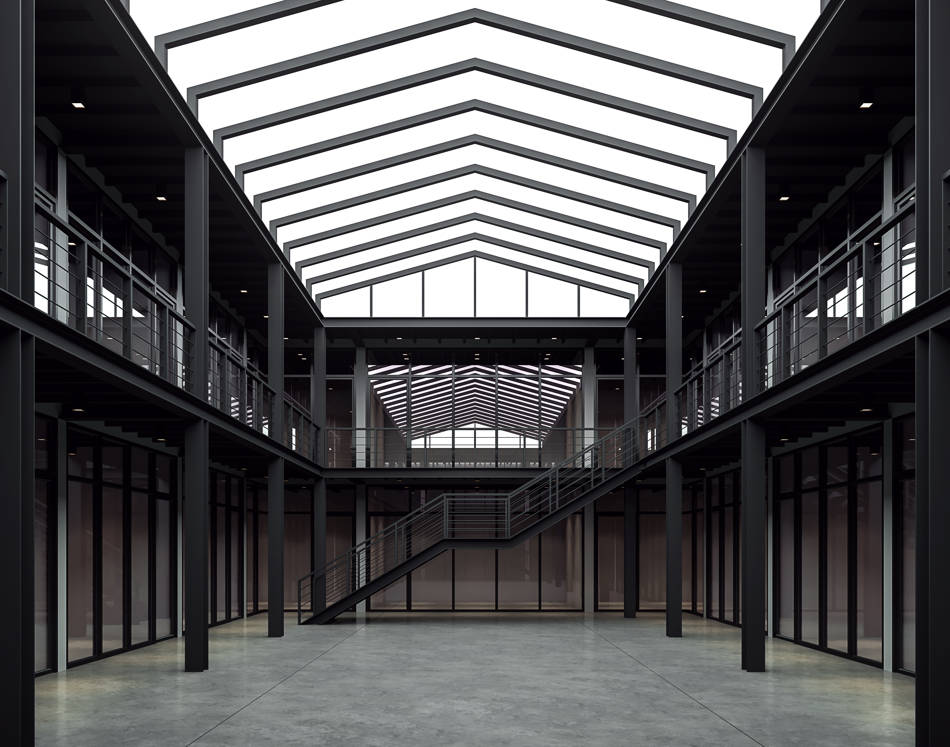
What is polished concrete?
Polished concrete, also called screed concrete, is actually a decorative finish, not a pure cladding. This product is mainly used in outdoor areas of car parks, shopping centres or sports fields and, to a much lesser extent, in some indoor rooms.
Polished concrete is a finish resulting from sprinkling a cementitious mortar with aggregates and then polishing the floor to a shine with a rotary polisher. This technique of polishing the floor is called trowelling.
Advantages of polished concrete
Polished concrete is designed to cover surfaces where the functionality of the flooring is more important than its aesthetics. Why? Because polished concrete is characterised by its great durability and resistance, two elements that make it ideal for covering industrial surfaces that are exposed to heavy traffic and weight. In fact, they are widely used for loading and unloading areas, as polished concrete flooring does not crack or chip.
In addition, polished concrete floors are very resistant to tyre rolling. This is why we see this type of finish so often in car parks and car parks.
Another quality of polished concrete floors is that their smooth and shiny surface prevents the accumulation of dust and dirt. A finish that also enhances the feeling of spaciousness.
Disadvantages of polished concrete
However, it is also important to know that polished concrete has a series of inconveniences and disadvantages to be taken into account. The following are the main ones:
Polished concrete can lose its shine over time due to very abrasive liquids such as industrial solvents. It will therefore have to be polished again.
It can end up cracking if expansion joints are not properly made or if the flooring is misused.
It can only be applied on horizontal surfaces.
This finish should be avoided in places with cold or very hot temperatures, as polished concrete is not a good thermal insulator.
The application process is time-consuming, as it requires building work and the use of machinery. In addition, it has joints.
As with temperature, polished concrete floors have poor sound insulation.
It is a material with low porosity and, in addition, it needs mesh for its structure.
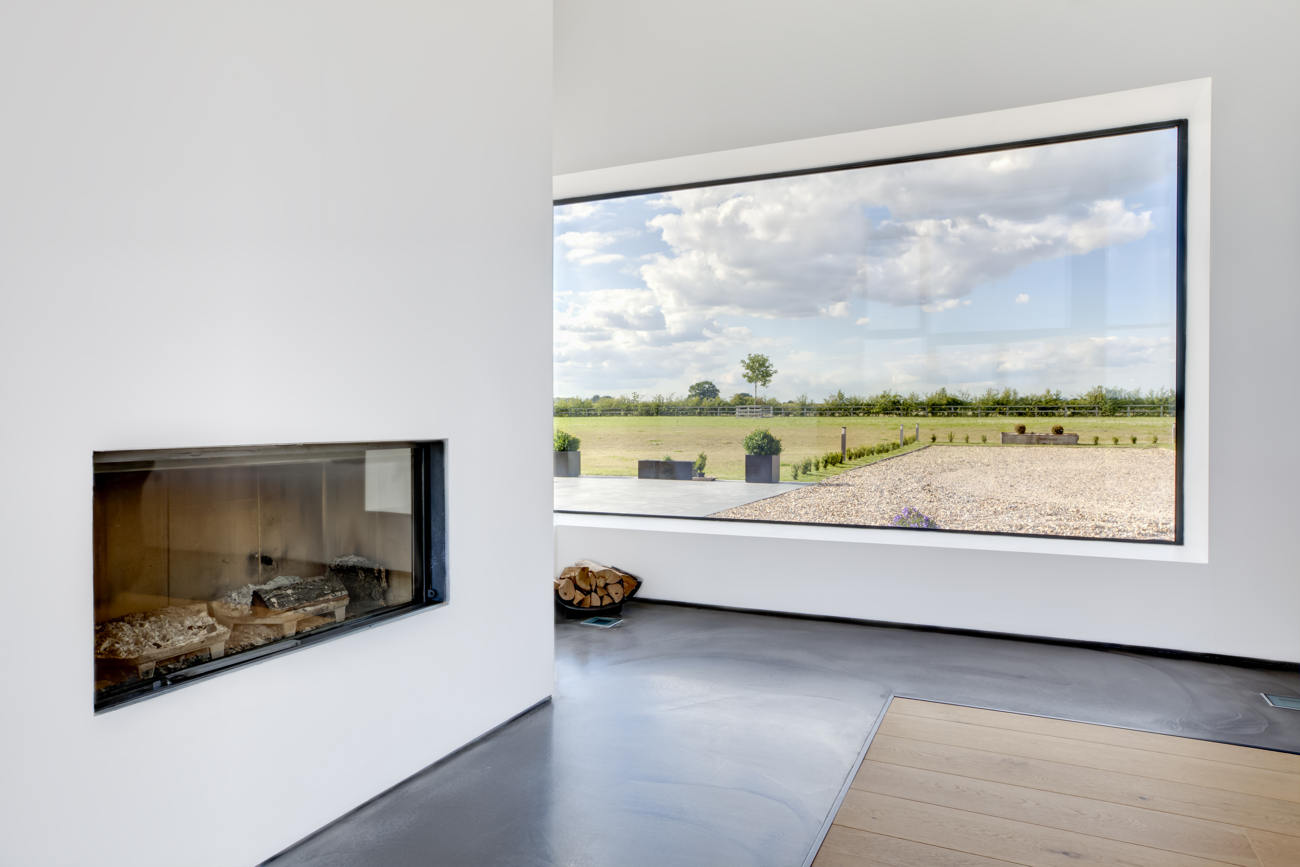
Polished concrete finishes
Although polished concrete is mainly associated with grey finishes due to the locations where it is usually applied, there is the possibility of choosing colours that are a priori more daring, such as black, red, green... Polished concrete is used in airports, car parks and garages, shopping centres and factories.
Polished concrete bathrooms
Polished concrete bathrooms do not exist. This type of finish is often confused with the use of other decorative coatings such as burnished concrete or a microcement washbasin. In fact, microcement is one of the most commonly used coatings to renovate this room due to the great possibilities of use it offers.
Microcement in bathrooms is perfect for lining shower trays or bathtubs, thanks to the waterproof and non-slip capacity it can achieve thanks to the use of specific sealants. But it can also be used to create shelves, bathroom furniture, walls and floors.
How to make a polished concrete floor
The installation of a polished concrete floor is not very different from the process of applying other types of concrete flooring. The components of sand, aggregates, cement and water are indisputable.
As is the fact that the concrete can be mixed either on site or with specialised concrete mixers. The latter alternative is the most suitable when large surfaces have to be covered. In the following, we explain step by step how to make a polished concrete floor correctly:
Step 1: Prepare the ground
Prepare the ground, making sure that there is no debris or dirt. If there is, remove and clean. Then check the floor levels, in case it is necessary to fill the surface.
Step 2: shuttering
Form the area to be paved with polished concrete. A process whose duration will vary depending on the square metres of surface.
Step 3: use a mesh
The next step is to strengthen the structure of the future polished concrete floor. This requires the use of a mesh, which will make the floor more resistant. In some cases, this may not be mandatory.
Step 4: pouring the concrete
Pour the concrete mix onto the pavement. It is very important in this step to smooth and level the surface, with the help of a ruler.
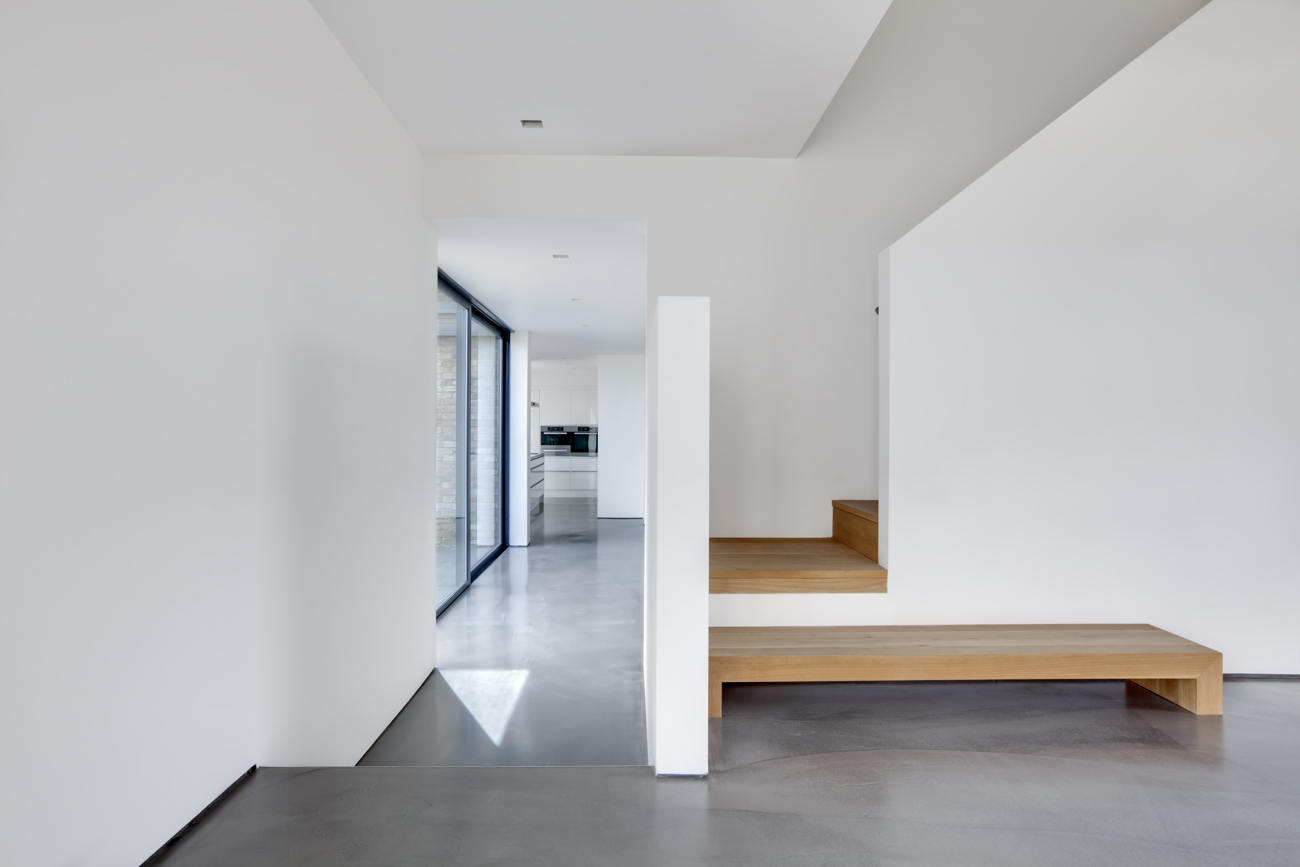
Step 5: checking the thickness of the slab
It is time to check the thickness of the slab, according to the level that we have used as a reference in the formwork step.
Step 6: concrete curing
Wait for the concrete to cure and dry properly. If necessary, use a float to smooth the screed for a much smoother finish.
Step 7: polishing the floor
To finish off a polished concrete floor, the surface needs to be polished to get that characteristic shine. This can be done with a chopper or a polishing machine.
Can polished concrete be applied outdoors?
The fact that polished concrete is a decorative covering that predominates indoors does not mean that its use is limited to such spaces. The strength and durability of this material make it an equally valid alternative for exteriors. An ambivalence which, despite the disadvantages of this material in comparison with, for example, microcement, is the reason for its popularity in recent years.
Thus, it is a decorative technique that can be applied in a multitude of outdoor spaces such as car parks, shopping centres, supermarkets, industrial warehouses, etc.
Price of polished concrete per m2
The price of polished concrete per square metre depends on several factors, including the dimensions of the floor to be covered and whether it is indoors or outdoors. In this sense, the final cost may be increased in some outdoor applications.
Similarly, the rates of each professional can cause significant price fluctuations as well as the time of year in which the work is carried out. Roughly speaking, the price of polished cement per m2 ranges between 40 and 50 euros approximately.
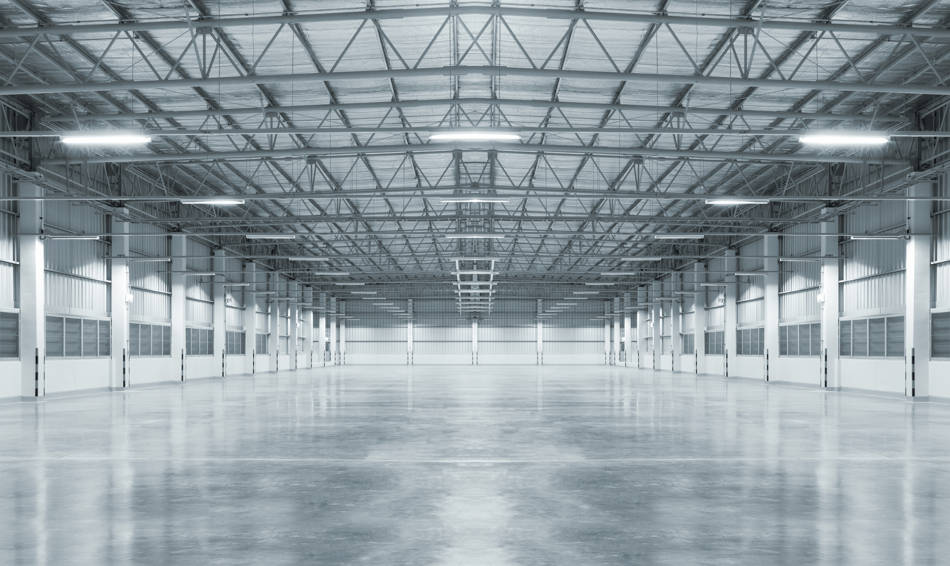
Differences between polished concrete and microcement
We are going to discuss the main differences between polished concrete and microcement.
1. Polished concrete is thicker than microcement.
The most noticeable difference between the two finishes is their thickness. Microcement is barely between 2 and 3 millimetres thick, which means that it can be applied on horizontal surfaces (floors, stairs, ceilings...) as well as on vertical surfaces such as walls. It is a thin building material so light that it can be applied anywhere without fear that the structure will be affected.
AThis is not the case with polished concrete, which is between 5 and 10 cm thick and whose application is reserved only for floors and pavements.
2. Polished concrete generates debris, microcement does not.
Another disparity between microcement and polished concrete relates to debris. Smoothed microcement is laid on the existing material, whether floor or wall. An excellent adherence that avoids building work and the debris that this entails.
This is the complete opposite of polished concrete, a finish that requires building work to completely lift the existing floor or paving and the use of machinery to do so.
3. The installation of polished concrete is much more time consuming.
This point is closely related to the previous one. As microcement does not require any building work, the application process is very fast. A procedure that in the case of polished concrete takes much longer.
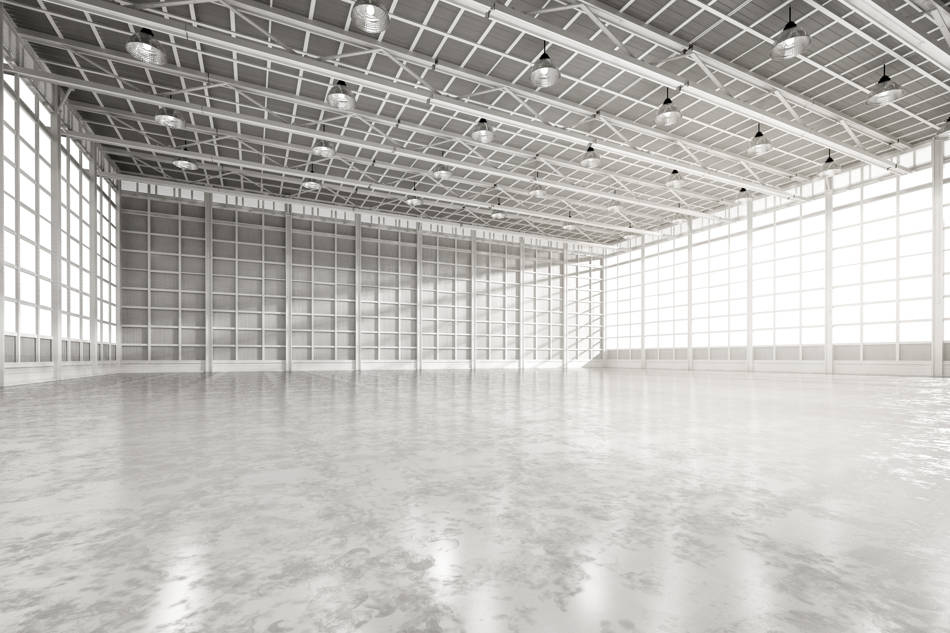
4. Polished concrete is only for floors, microcement also for walls.
While the versatility of microcement allows it to be used as a wall and floor covering, polished concrete can only be applied on floors. A differentiation which, logically, has boosted the popularity of the former to the detriment of the latter.
5. Compatibility vs. incompatibility with underfloor heating
Underfloor heating is a great alternative to radiators and central heating because of its benefits. However, this system is not compatible with any coating.
Microcement, which has a high thermal conductivity, is perfectly compatible with underfloor heating. In fact, it is one of the most recommended construction materials. Here you will find everything you need to know. A quality that polished concrete cannot boast.
6. Only polished concrete needs expansion joints
Polished concrete requires expansion joints, approximately every 4 to 5 metres. Microcement, on the other hand, is a continuous covering and, therefore, no expansion joints need to be made. This is why the use of smoothed microcement has increased in interiors to the detriment of polished concrete.
7. Microcement is more versatile than polished concrete
Microcement is not only a continuous coating that does not require building work or expansion joints, but it is also quicker and easier to apply.
But not only because of this, but also because smoothed microcement also provides the security of being a coating with excellent durability and resistance not only to traffic like polished concrete, but also to knocks, wear due to abrasion, chemical products or scratches, among others.
And, above all, because offers more decorative solutions as it can be applied on any surface (horizontal or vertical) and material (concrete, tiles, tiles, ceramic...). A wider range that makes it easier for microcement to be used in interiors and exteriors, both in private homes and in premises, businesses and other companies. In short, for all these reasons and more, microcement is much more complete than polished cement.